美しい革をつくる現場へ。革きゅん工場見学レポート。
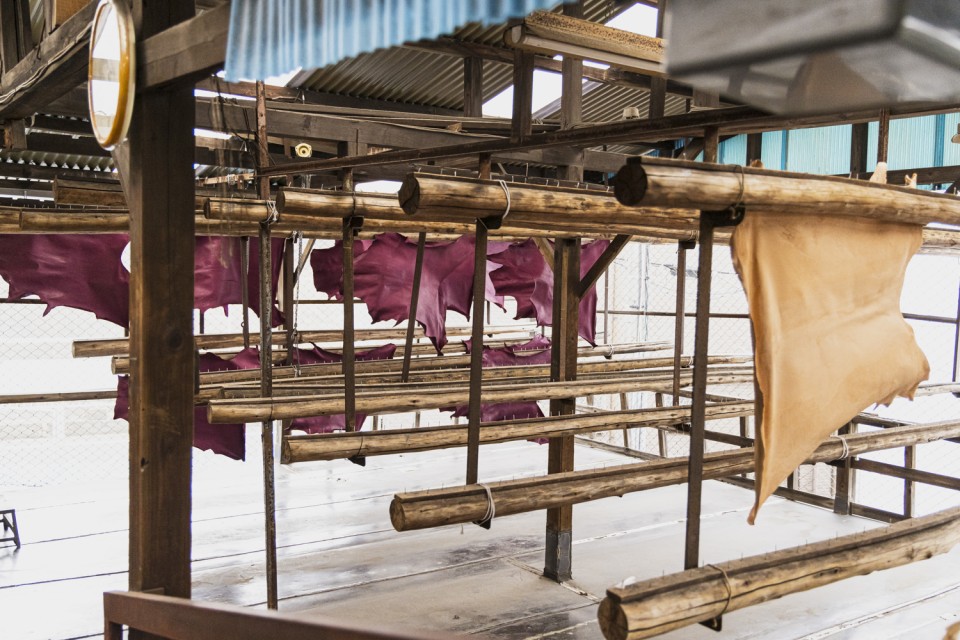
革きゅん工場見学企画の2回目が、2023年11月に開催された。動物の命からいただいた“皮”が“革”へと生まれ変わる現場に触れる貴重な機会に、多くの読者が参加した。
今回訪れたのは、東京都墨田区にあるタンナー(製革業者)、小笠原染革所。皮革の買い付けから鞣し、染色から仕上げまで手がけている。東京では最大級のスキンタンナリーといわれている小笠原染革所は、1903(明治36)年創業。100年以上の歴史をもつこの工場で、創業当時は手袋用の革をつくっていたという。
羊革や山羊革、鹿革など、小判ものといわれる革を製造する機械が充実し、靴や鞄、小物などに使われる革をつくりだしている。なかでも衣類に用いられるソフトな手触りの革は業界でも一目置かれており、海外のファッションブランドから依頼を受けることも。そんな⼩笠原染⾰所の4代目社長である小笠原誉行さんが、工場内を案内してくれた。
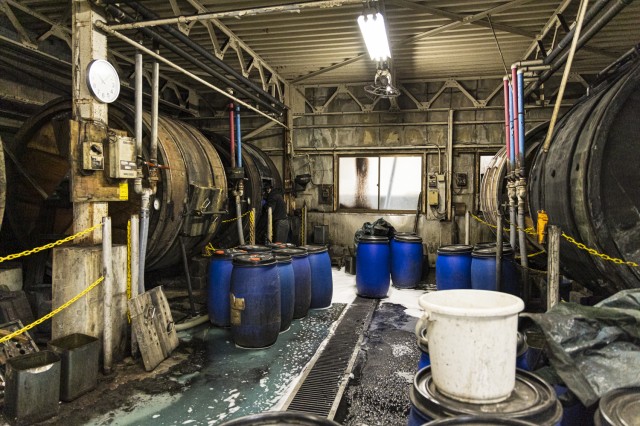
「ドラム」または「太鼓」と呼ばれる、鞣しや染色、加脂などさまざまな工程に用いられる回転式の機械。小笠原染⾰所では、羊の皮であれば100枚ほどが入る小さなドラムと500枚ほどが入る大きなドラムの2種類が稼働している。
歴史あるタンナーで目の当たりにする、革づくりの工程。
⼩笠原染⾰所では鞣しから染色、塗装など仕上げ加工まで幅広い工程を手がけている。長い歴史が刻まれていることを感じさせる、重厚感のある機械がずらりと並ぶ工場内は、ものづくりの現場らしい活気にあふれている。工場に足を踏み入れた参加者たちからも、思わず感嘆の声が上がる。
工場に届いた原皮が、数々の工程を経て本革になるまでにかかる期間は、およそ1カ月。工場の1階には大きな木製のドラムが並び、この場所で本革が生み出されていく。
「革づくりは、いわば料理のようなものです。皮に色を入れたり、脂を入れたり、硬さをもたせたりしていく作業は、革のキャラクターを生み出す大切な工程です。夏と冬に仕入れた皮革では染まり方が違うなど、なかなか思い通りにならないこともあるので、日々データを取って研究しています」
4代目として小笠原染革所を継ぐ前、イギリスの大学に留学して革づくりの基礎を学んだ小笠原さんは、微妙な調整が必要な染色工程において、現地で実践して学んだノウハウを生かしている。勘や目分量ではなく、データを蓄積して合理的な方法をアップデートしていく作業のなかで、独自のレシピが生まれていくという。皮革の種類はもちろんのこと、色によっても染まり方がまったく違うそうで、「なかでも黒色がもっとも難しいんです」と小笠原さんは話す。
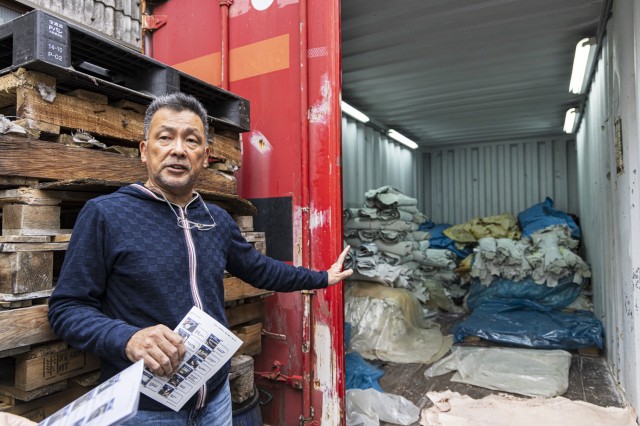
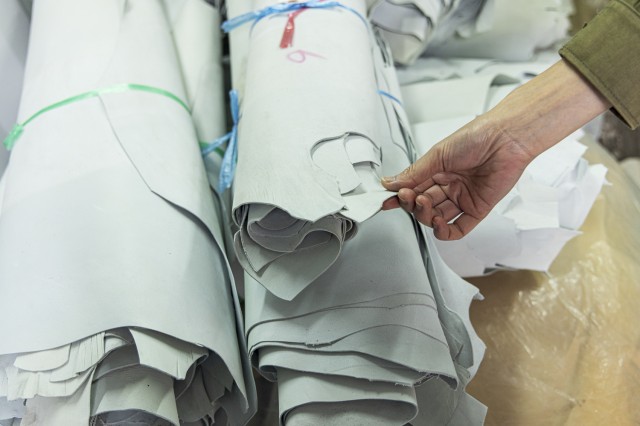
革の保管庫を案内してくれた小笠原さん。クロム鞣しを施して乾燥させた状態の革は青味がかった白色で、「クラスト」とも呼ばれる。この後の工程次第でさまざまに表情を変える。
鞣しの工程では、朝に皮と鞣し剤をドラムに入れたら夕方まで回し続ける。この工程には水を多く使うため、古くからタンナーの工場は河川に近いエリアに建てられてきた歴史がある。⼩笠原染⾰所では、できるだけ環境に負担をかけない生産方法を採用しており、工場敷地内には排水処理施設も完備。自社工場から排出される水はすべて適切に処理されている。
参加者が見学したコンテナの中には、淡く青味がかった見た目から「ウェットブルー」と呼ばれる、クロム鞣しを施した革が保管されていた。クロム鞣しされた革は柔軟性や伸縮性、耐熱性に優れた革に仕上がるという。できたての革を目の当たりにした参加者が、「クロム鞣しは短期間で効率的にできる方法という知識があったのですが、とても労力をかけてつくられているんだなと思いました」と驚く。
続いて、染色の工程を見学。染色されたばかりの革は、たっぷりと水分を含んでいる。その水分を絞る工程は「セッティング」と呼ばれ、専用の機械にかけられてしっかり水が絞られる。革を適度に引っ張りながら伸ばすことで、革を平らにして形を整える工程でもあるという。
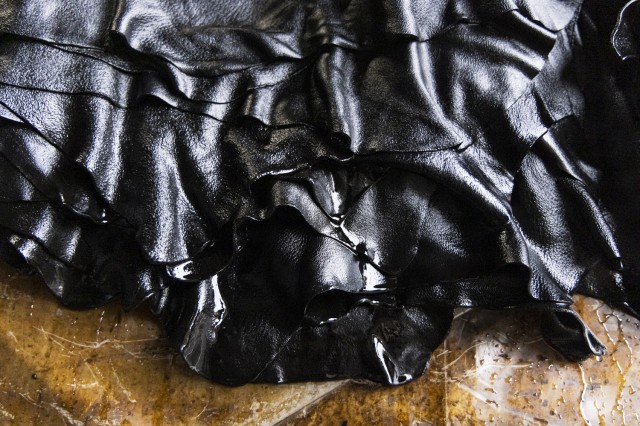
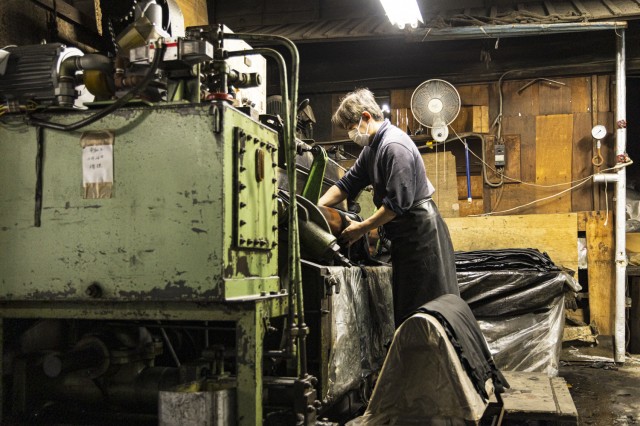
染色を終えて水分をたっぷりと吸った革は、艶やかで美しい。この革は、水分を絞る「セッティング」の工程にかけられる。
仕上げの工程を経て、バリエーション豊かな革が生まれる。
セッティングを経て、しわなどを伸ばして平らになった革は、2階の干し場へ。風通しのよい空間にいくつもの竿が掛けられた干し場では、さまざまな色に染められた革が風に揺れている。参加者たちは干し場に並ぶ革の形状からそれがどんな動物の革か想像を膨らませながら、実際に革に触れて感触を確かめていた。「革の種類によって触り心地が全然違うのに驚きました」と、参加者のひとりが言う。
小笠原染革所では、世界中から皮革を厳選して仕入れている。山羊はインドやパキスタン、バングラデシュなどから、羊はスペインやトルコなど、鹿はニュージーランドが中心という。「同じ動物でも、仕入れ先によって出来上がるレザーの風合いは全然違うものになります。オスかメスか、季節によっても皮質は微妙に変わってきます。もちろん100%食肉の副産物である皮を使用しています」
小笠原さんが言うように、皮は私たちが口にする肉と同じように動物の命からいただいたもの。食肉の生産過程で発生する皮を捨てることなく、革に生まれ変わらせてレザーアイテムに仕立て、それを長く愛用することは、まさにエコでサステナブルなこと。参加者のひとりである大学生から、「狩猟された動物の皮は、利用できないのですか?」という質問があった。
「もちろん不可能ではないけれど、難しい課題もあります。タンナーに届く前に皮を腐らないよう適切に処理することができれば、狩猟された動物の皮ももっと利用方法が広がるでしょうね」と小笠原さん。
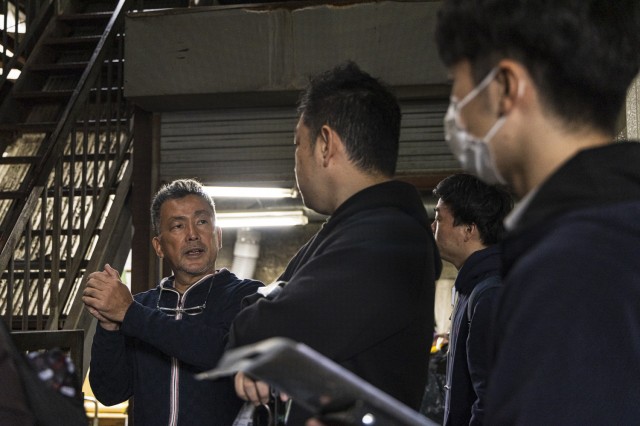
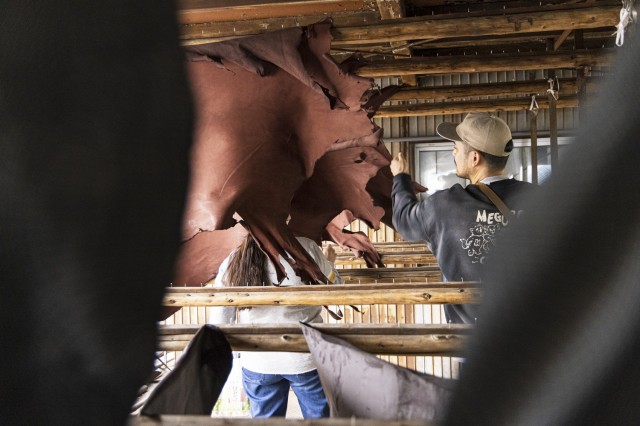
原皮の産地や、それぞれの革が持つ特徴についての質問が飛び交う。干されている革の鮮やかな発色も、参加者の心をとらえていた。

「黒色の出し方がもっとも難しい」と教えてくれた小笠原さん。30種類以上もの染料を調合し、顧客が求めるベストな色合いを実現させるべく日々研究している。
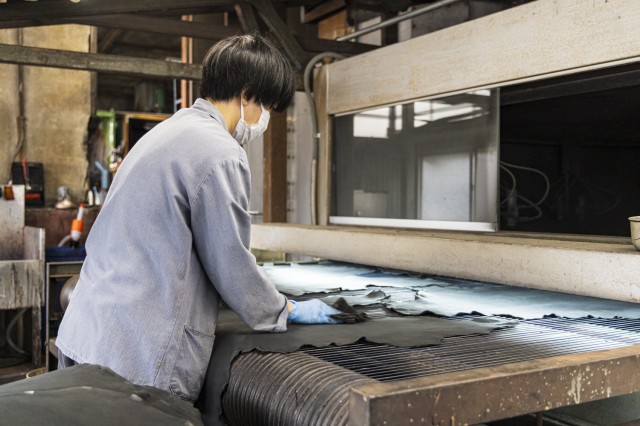
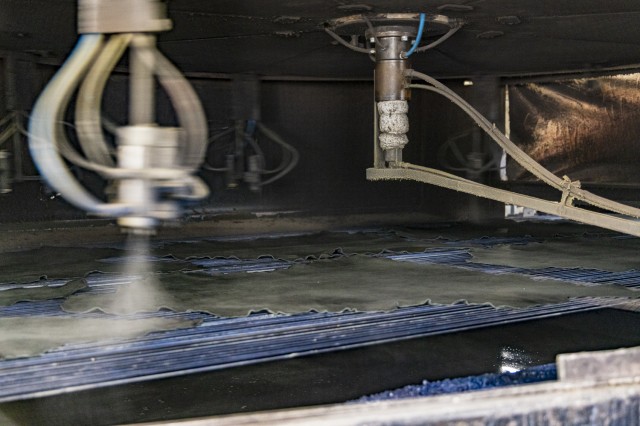
革を仕上げていく時は、機械を使って塗装作業をしていく事が多い。
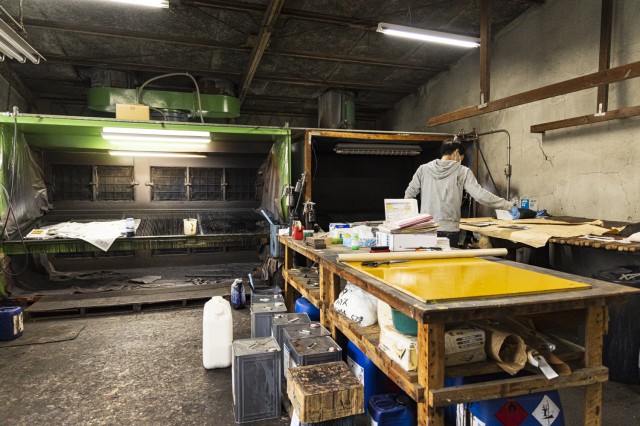
機械に入らない大きな革を扱う時や、染料や顔料を調合しながら色合わせのテストをする時は、塗装を手作業で行う場合もある。
自然乾燥後は、機械を使って革に振動を与え、もともと革がもつしなやかさを大切にしながら適度な柔らかさを出す「ステーキング」や「バイブレーション」と呼ばれる工程でしっかりと揉みほぐして柔らかくしていく。さらに、もっとソフトにしたり、シボと呼ばれる模様を出すことができるのが「バタ振り」の工程だ。機械のアームに革を挟むと、アームが上下にバタバタと動く。このユニークな工程に、参加者たちからも「おもしろい!」と歓声が上がる。
「“柔らかくする”といっても、これが本当に難しいんです。革を叩いて繊維をほぐすほど柔らかくなっていくのですが、革ならではのしなやかな硬さは残さなくてはならない。人が触れた時に心地よいと感じるような風合いや、本革らしいしなやかさを出す作業が必要なのです」。小笠原さんの真摯な言葉に参加者たちが耳を傾ける。

オーダーに合わせて革の柔らかさをコントロールする作業を参加者に説明する小笠原さん。
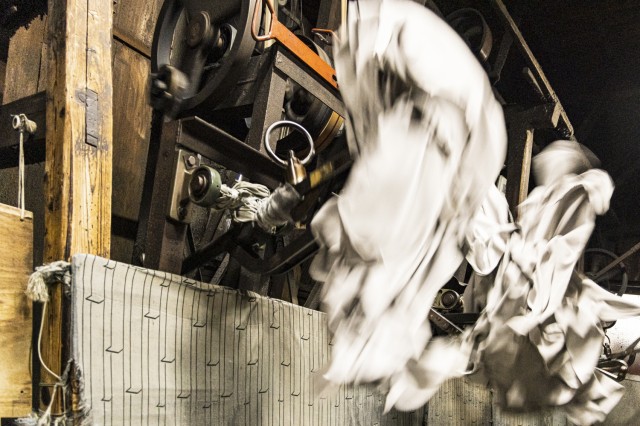
アームに数枚の革を挟んで、上下にバタバタと振る「バタ振り」と呼ばれる工程。
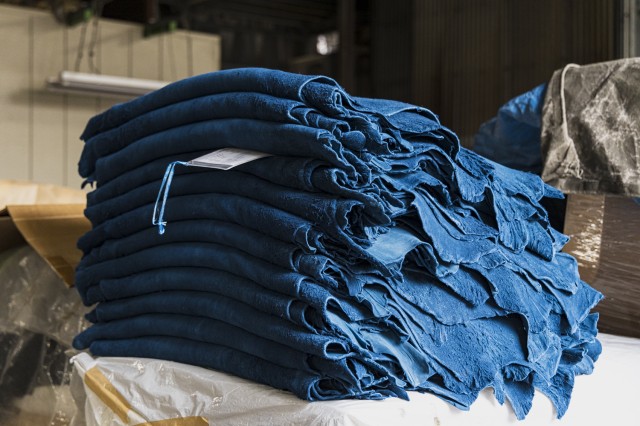
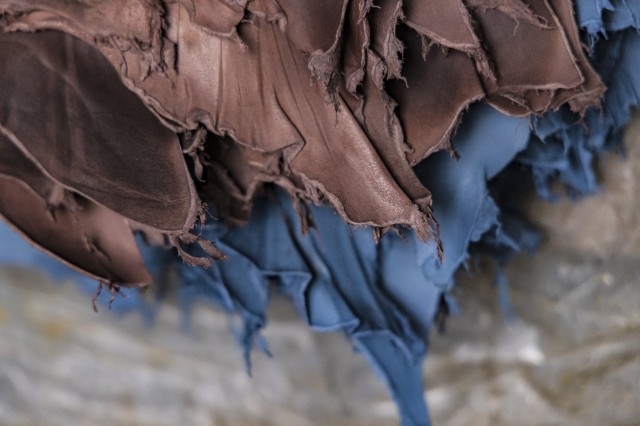
鮮やかに染められた革。30種類以上ある染料のひとつひとつの特徴をつかみ、その革の特性に合った調合をするのもタンナーの技術だ。
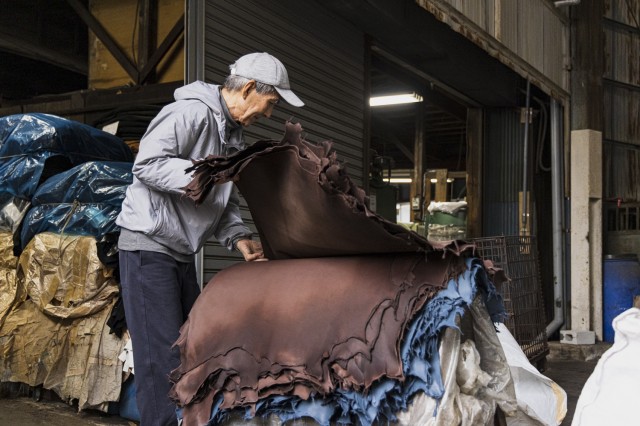
出来上がった革からは、本革らしい香りが漂っている。小笠原染革所では、腕利きのベテラン職人や修行中の若手職人がともに働いている。
100年以上の歴史を誇る小笠原染革所にて、革をつくる職人たちの仕事を目の当たりにした参加者たちは、革に対する印象が変わったと口々に言う。靴修理のアルバイトをしているという学生は「普段から革に触れていますが、革がどのようにつくられるかまったく知らなかったので、勉強になりました。こんなに多くの工程と時間を経てできあがる革を、修理する立場としても大切にできたらと思いました」と語った。レザーアイテムのブランドを手がけるクリエイターは「ものづくりに携わっているので、どうしても革素材の製造工程が見たくて参加しました。柔らかさのバリエーションも微妙な色の違いも、すべてが職人技。感激しました」と話してくれた。レザーの風合いが好きで参加したという女性は「本革がエコなものだと知ることができてよかったです。動物の命を無駄にしない、素晴らしいことだと感じました」と笑顔を見せた。
「タンナーの仕事は料理のよう」と表現する小笠原さんの言葉どおり、革をつくり出すための独自のレシピ研究に努力を惜しまない職人たちの姿は、参加者たちの心を打ったようだ。受け継がれた技術とあくなき探究心によって、きっと今日もまた美しい風合いのレザーが生み出されているだろう。
小笠原染革所
東京都墨田区墨田4-31-7
https://ogasawara-leather.jp/
photography: Mirei Sakaki, text: Miki Suka